A wooden cutting board from plllank is not just any cutting board. As a recognized craftsman - decision by FPS Economy, Craftsmen Committee, July 17, 2023 - the board is worked on from start to finish with care, knowledge and attention to detail. Finally, plllank delivers a straight, flat, correctly glued, food-safe, unique, stylish, functional, local and sustainable hardwood cutting board. Read below how this process works.
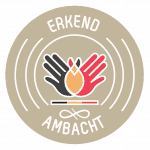
STEP 1
Raw Planks from Local Sawmills
Everything depends on a good foundation. The raw wood is purchased from local sawmills. With my background as a bio-engineer in forest and nature management, I have extensive knowledge of wood. Only the most qualitative and suitable species for cutting boards are used. These are carefully selected for both structure, quality and aesthetics.
STEP 2
Planing and Flattening
The raw boards from the sawmill are planed and flattened into perfectly flat and squared surfaces on the planing machine in our own workshop. Then they are brought to thickness and planes made parallel to each other with the thicknessing machine.
STEP 3
Sawing
The planed boards are cut to the desired dimensions with the table saw. Here the size of the cutting board is determined and boards are sawn into thinner slats to determine the pattern. Even for end-grain cutting boards, the sawing already plays a major role.
STEP 4
Straightening
All surfaces of the sawn boards and slats that will be glued are first made perfectly straight and smooth with the thickness sander or cylinder sander and cleaned with compressed air. This ensures a much better surface to glue and stronger bond.
STEP 5
Bonding
Bonding is done with food-safe wood glue that provides waterproof joints between the wood. Wood glue obtains its strength through pressure. Gluing with correct clamping is therefore very important. Parallel clamps are used over the entire board to obtain uniform pressure. The site of bonding will finaly be many times stronger than the wood itself.
STEP 6
Cutting board Flattening
The cutting board is removed from the clamps and smoothed for the first time. All excess glue is removed with a specific glue scraper after which the cutting board passes through the thicknesser. This produces two perfectly straight surfaces and a parallel top and bottom surface. Large cutting boards such as butcher blocks are flattened either with a milling jig or with the in-house CNC machine.
STEP 7
Sawing
The cutting board is sawn to the final size if it is a edge-grain cutting board. If end-grain cutting board, here follows another sawing and gluing (back to step 3). This allows for interesting patterns, but because of the multiple operations, results in a higher price.
Every raw board that is sawn for cutting board construction is already inspected with a strict eye for defects. Think of knots due to ingrown branches or cracks due to the drying process. If such a defect is still observed during the construction of the cutting board, the cutting board is rejected, re-sawn if it is on the top surface, or properly sealed if it is on the bottom surface.
STEP 8
Sanding, sanding, sanding....
First, the entire cutting board goes through the thickness sander where it is sanded perfectly flat at the top and bottom with 80-grit paper. Then it is manually sanded with an eccentric sander in 80, 120 and 180 grit. After this last grit, the cutting board is made completely wet. This ensures that the fibers straighten / set up after which they are sanded again with 180-grit paper. This step ensures that the board remains perfectly smooth when it is wetted afterwards and only benefits hygiene.
STEP 9
Mirror Finish
In a second sanding phase, further sanding is done with 240, 320 and 500 grit. end-grain is polished with 1000 grit to achieve a mirror finish. This super-smooth surface is not only beautiful, but also makes it much harder for moisture to penetrate which again makes for improved hygiene and food-safe wooden cutting board.
STEP 10
Oil and Wax
Finally, the finishing stage follows. The plllank logo is lasered onto the cutting board and each board is immersed in a bath of mineral oil. Unlike rubbing with oil, this ensures better impregnation of the oil into the cutting board. In this process, all the vessels of the wood are filled and the oil provides resistance to moisture and consequently bacteria.
Then each cutting board is treated with a final top wax. This with a wax according to house recipe based on mineral oil and sterilized beeswax that is carefully rubbed in two stages. Internally protected by mineral oil and externally protected by the perfectly sanded surface and natural top wax layer.
Each wooden cutting board from plllank comes with a jar of homemade wax and microfiber glove to rub it in.