Ein Holzschneidebrett von plllank ist nicht irgendein Schneidebrett. Als anerkannter Handwerker - Beschluss des FÖD Wirtschaft, Ausschuss der Handwerker, 17. Juli 2023 - wird das Brett von Anfang bis Ende mit Sorgfalt, Wissen und Liebe zum Detail bearbeitet. Am Ende liefert plllank ein gerades, flaches, korrekt verleimtes, lebensmittelechtes, einzigartiges, stilvolles, funktionelles, regionales und nachhaltiges Hartholzschneidebrett. Lesen Sie unten, wie dieser Prozess funktioniert.
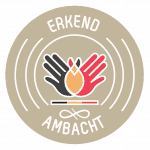
SCHRITT 1
Rohe Bretter von lokalen Sägewerken
Alles hängt von einer guten Grundlage ab. Das Rohholz wird von örtlichen Sägewerken bezogen. Mit meinem Hintergrund als Bio-Ingenieur in der Forst- und Naturwirtschaft verfüge ich über ein umfangreiches Wissen über Holz. Es werden nur die hochwertigsten und am besten geeigneten Holzarten für Schneidebretter verwendet. Diese werden sorgfältig nach Struktur, Qualität und Ästhetik ausgewählt.
SCHRITT 2
Hobeln und Nivellieren
Die rohen Bretter aus dem Sägewerk werden in unserer eigenen Werkstatt auf der Hobelmaschine in perfekt ebene und quadratische Flächen gehobelt und geglättet. Anschließend werden sie auf Dicke gebracht und die Oberflächen mit der Dickenhobelmaschine parallel zueinander ausgerichtet.
SCHRITT 3
Sägen
Die gehobelten Bretter werden mit der Tischsäge auf die gewünschten Maße zugeschnitten. Hier wird die Größe des Schneidbretts festgelegt und die Bretter werden in dünnere Latten gesägt, um das Muster zu bestimmen. Auch bei Kopfholzschneidebrettern spielt das Sägen bereits eine große Rolle.
SCHRITT 4
Perfekte Rechte
Alle Oberflächen der gesägten Bretter und Latten, die verleimt werden sollen, werden zunächst mit der Dicken- oder Zylinderschleifmaschine vollkommen gerade und glatt gemacht und mit Druckluft gereinigt. Dies sorgt für eine viel besser verklebbare Oberfläche und eine stärkere Verklebung.
SCHRITT 5
Bindung
Die Verklebung erfolgt mit lebensmittelechtem Holzleim, der für wasserdichte Verbindungen zwischen dem Holz sorgt. Holzleim erhält seine Festigkeit durch Druck. Die Verleimung mit der richtigen Einspannung ist daher sehr wichtig. Um einen gleichmäßigen Druck zu erzielen, werden parallele Klammern über das gesamte Brett verwendet. Die Leimstelle ist am Ende um ein Vielfaches stärker als das Holz selbst.
SCHRITT 6
Schneidebrett Abflachung
Das Schneidebrett wird aus den Klemmen genommen und zum ersten Mal geglättet. Der gesamte überschüssige Leim wird mit einem speziellen Leimschaber entfernt, danach wird das Brett durch die Dickenhobelmaschine geführt. Auf diese Weise entstehen zwei vollkommen gerade Oberflächen und eine parallele Ober- und Unterseite. Große Schneidbretter wie Metzgerblöcke werden entweder mit einer Fräsvorrichtung oder mit der hauseigenen CNC-Maschine geglättet.
SCHRITT 7
Sägen
Das Schneidebrett wird auf die endgültige Größe gesägt, wenn es sich um ein Langholzschneidebrett handelt. Handelt es sich um ein Kopfholz-Schneidebrett, wird es erneut gesägt und verleimt (zurück zu Schritt 3). Dies ermöglicht interessante Muster, führt aber wegen der vielen Arbeitsgänge zu einem höheren Preis.
Jedes rohe Brett, das für die Herstellung eines Schneidebretts gesägt wird, wird bereits mit einem strengen Auge auf Fehler geprüft. Dazu gehören Äste, die durch eingewachsene Äste verursacht werden, oder Risse, die durch den Trocknungsprozess entstehen. Wird bei der Herstellung des Schneidebretts dennoch ein solcher Fehler festgestellt, wird das Schneidebrett aussortiert, neu gesägt, wenn es sich um die Oberseite handelt, oder ordnungsgemäß versiegelt, wenn es sich um die Unterseite handelt.
SCHRITT 8
Schleifen, schleifen, schleifen...
Zunächst durchläuft das gesamte Schneidebrett die Dickenschleifmaschine, wo es auf der Ober- und Unterseite mit 80er-Papier perfekt plan geschliffen wird. Anschließend wird es manuell mit einer Exzenterschleifmaschine in den Körnungen 80, 120 und 180 geschliffen. Nach diesem letzten Schliff wird das Schneidebrett vollständig nass gemacht. Dies sorgt dafür, dass sich die Fasern aufrichten und anschließend erneut mit 180er-Papier geschliffen werden. Dieser Schritt sorgt dafür, dass das Brett im nassen Zustand vollkommen glatt bleibt und dient ausschließlich der Hygiene.
SCHRITT 9
Spiegelnde Oberfläche
In einer zweiten Schleifphase wird mit 240er-, 320er- und 500er-Papier weiter geschliffen. Kupferholz wird mit 1000er-Papier poliert, um eine spiegelglatte Oberfläche zu erhalten. Diese superglatte Oberfläche ist nicht nur schön, sondern erschwert auch das Eindringen von Feuchtigkeit, was wiederum zu einem hygienischeren und lebensmittelechteren Holzschneidebrett führt.
SCHRITT 10
Öl und Wachs
Schließlich folgt die Veredelungsphase. Das plllank-Logo wird auf das Schneidebrett gelasert und jedes Brett wird in ein Mineralölbad getaucht. Im Gegensatz zum Einreiben mit Öl wird dadurch eine bessere Imprägnierung des Öls im Schneidebrett gewährleistet. Dabei werden alle Gefäße des Holzes gefüllt und das Öl bietet Widerstand gegen Feuchtigkeit und damit auch gegen Bakterien.
Dann wird jedes Schneidebrett mit einem abschließenden Deckwachs behandelt. Dies mit einem Wachs nach Hausrezept auf der Basis von Mineralöl und sterilisiertem Bienenwachs, das in zwei Stufen sorgfältig eingerieben wird. Innen geschützt durch Mineralöl und außen geschützt durch die perfekt geschliffene Oberfläche und die natürliche Deckwachsschicht.
Jedem Holzschneidebrett von plllank liegt ein Glas mit selbstgemachtem Wachs und ein Mikrofaserhandschuh zum Einreiben bei.